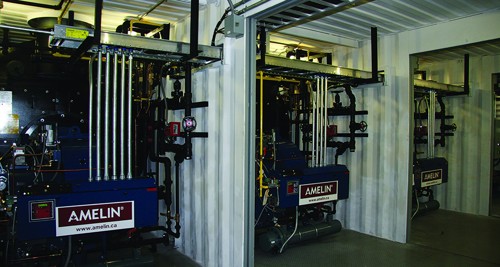
Amelin
The customer needed a system that would produce 20 tons of steam per hour (44,000 lbs) and could be built in the U.S., disassembled, then shipped to Russia and reassembled on-site. Continue Reading
In this case, the subject of our efforts was pretty much every large-scale boiler operation out there. When a large boiler needs to be taken offline for repairs, maintenance, or replacement, the only thing that will replace it is a large-scale rental boiler. While it’s often possible to connect a rental boiler to the existing water treatment system, many rental situations don’t have sufficient deaerating and softening capabilities, especially in remote areas.
Big boilers need a lot of water. Sometimes, they need so much makeup water that they get ahead of what the water treatment system can supply. This often means feeding in water that hasn’t been properly softened or stripped of oxygen. Allowing hard, oxygenated water to enter the boiler’s pressure vessel will inevitably increase the risk of scale and corrosion. What the world needed was an easy way to soften and deaerate feedwater on a large-enough scale that even the thirstiest boilers at high demand would have plenty of makeup water available. Enter WARE ingenuity.
WARE needed to create a portable, rentable water softening and deaeration system that was larger than anything else out there, capable of supplying full makeup water at 200,000 pph.
How do you design a system that can soften and deaerate enough water to supply a 200,000 pph boiler with full makeup water and up to ten minutes of reserve, and then make it fully self-contained, and easy to transport?
We have over 70 years of experience in the boiler business, and some of the industry’s most highly skilled technicians. Together, we’ve designed and engineered a mega-milestone in the boiler industry: A 200,000 pph deaerator with its own 3.6-million-grain water softener and a full-capacity pumping system, plus all the necessary piping and valves, all in a single custom 57-foot trailer.
Other portable rental softeners and deaerators come in a skid configuration, which is technically portable, but not always easy to move. These setups typically include an exposed overhead tank on an I-beam frame to hold makeup water. In colder temperatures, this setup requires a substantial outlay of supplies and hours to properly insulate all the pipes, gaps, and spaces in a configuration that is almost entirely exposed to the elements. Furthermore, all electrical panels must also be weatherproofed, or else they can develop leaks over time that can lead to shorts, and costly downtime.
By contrast, WARE’s 200,000 pph deaerator, 3.6-million-grain softener, and full-capacity pumping system arrive ready to go in their own self-contained, insulated, fully enclosed boiler room. No exposed pipes, no exposed tanks, no exposed panels. It’s everything you need in a one-stop, no-worry solution. Forget about the weather, just connect the steam lines, water lines, power lines, and drains, and you’re good to go with full makeup at 200,000 pph. No cranes or forklifts required.
For more information, contact our rental department today.
The customer needed a system that would produce 20 tons of steam per hour (44,000 lbs) and could be built in the U.S., disassembled, then shipped to Russia and reassembled on-site. Continue Reading
WARE is an industrial & commercial boiler rental and service company that specializes in sales, service, valve repair, rentals, parts, turn key and boiler training.