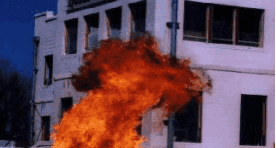
Zussman Village
Zussman Village – Urban Combat Training Facility Ft. Knox, Ky Continue Reading
Over the past 3 years, WARE has been developing a long-term rental boiler solution for Hill Air Force Base, boilers that were finally commissioned in September of 2024. This massive boiler system (two main boilers plus a backup) highlighted WARE’s expertise and professionalism, while helping the Air Force keep our country safe.
Hill Air Force Base, located in Davis County, Utah, is a major United States Air Force Base that is home to some of America’s most advanced fighter and cargo airplanes including the F-35 Lightning, the A-10 Warthog, and the F-22 Raptor. Hill is also home to the 748th Supply Chain Management Group that serves in supply and logistics roles around the globe.
Hill Air Force Base needed a long-term rental boiler configuration that could deliver 168,000 pph while running on #2 Fuel Oil or Natural Gas. But there were space and emission requirements that made the project more of a challenge.
WARE’s original plan was to supply Hill with four trailer-mounted Victory boilers each putting out 82,500 pounds of steam per hour, along with a skid-mounted deaerator and water softener. Unfortunately, space constraints necessitated a more customized solution that would require a smaller footprint of only three boilers, with no additional space available for water treatment or deaeration equipment. And energy input requirements limited the options available.
There were several obstacles that made the job a challenge. First, all three boilers had to fit into the existing equipment footprint, and that had to include deaerator and water softener equipment because there was no additional space allotted for any external water treatment equipment. Second, the entire setup had to run at an elevation of 4,500 feet, where the air is thinner and making proper combustion becomes an obstacle. But one of the biggest challenges had to do with the input BTUs and emissions. Once initial planning had begun, the specifications were revised; to avoid more detailed and stringent monitoring regulations, the boilers could consume no more than 99,000,000 BTUs per hour and generate less than 9ppm NOx. That meant that the boilers had to put out a lot of steam with substantially less energy flowing into them.
WARE’s boiler pros are experts at everything steam-related, and that includes completely customized, designed-from-scratch boiler solutions for specific asks. After 8 different designs were considered, construction began on the boilers that would solve the problem.
Using reliable Victory Energy boilers as a starting point, WARE combined a few ingenious ideas that had not yet been tested in the real world. In the end, WARE was able to answer the Call of Duty for Hill Air Force Base and delivered exactly what they needed.
Using a Victory Energy 82,500 pph boiler as a starting point, WARE constructed an entirely custom-made setup that included a 3.6-million-grain onboard water softener, full deaeration, and all the high-capacity pumps necessary to keep the water moving. The water treatment system was all installed in a specially designed 57’ trailer. While each boiler is 3 tons heavier than the original design, it all still fits within the same space. Furthermore, the system is capable of providing 100% makeup water even as the boilers ran at full rate.
To close the gap between output requirements and input limitations, WARE installed economizers on the boilers that could each squeeze an additional 10,000 pph out of every cubic foot of fuel. Furthermore, to compensate for the thinner air at that elevation, WARE further equipped each boiler with a larger fan and a 250hp blower motor to move more air through the system to keep the burners fed.
Each boiler also received a sophisticated control system that constantly monitors system performance, fine-tuning the combustion to maximize energy while minimizing NOx levels as much as possible. Before the advent of advanced boiler control systems, there’s no way any boiler could have met the Air Force’s stringent requirement. But today’s control systems can get a boiler right to the edge of optimum performance, and then keep it there with near-constant micro-adjustments on a second-by-second basis.
Upon initial testing, the custom units delivered as expected, providing 85,000 pph of steam with NOx levels just over 7ppm. Three of these custom units were delivered, two for regular operation and one as a backup. This achievement was significant, because up to that point, no other boiler company out there had ever been able to get 85,000 pph out of a mobile unit while staying under 9 ppm NOx. Not to mention doing it with onboard, trailerized water softening and treatment, in a limited space. But WARE and Victory Energy made it happen.
WARE even conquered the challenge of transporting these massive boiler systems to Utah, using a series of 57-foot trailers to move the boilers to their intended destination.
Zussman Village – Urban Combat Training Facility Ft. Knox, Ky Continue Reading
WARE was able to supply all the steam units requested (25), as well as the installation and maintenance required for the units. Continue Reading
Rental of Three 75,000 pph boilers with economizers Continue Reading
Two 70,000 lb/hr Water Tube Boilers - Continue Reading
WARE is an industrial & commercial boiler rental and service company that specializes in sales, service, valve repair, rentals, parts, turn key and boiler training.